The Thai electronics industry is forecast to return to healthy rates of growth over the three years from 2021 to 2023 thanks to a number of different developments on the technology front. In particular, demand for electronics parts will be boosted by the development and rollout of 5G technology and the need for equipment that supports this, and by the increasing market penetration of smart cars, which will in turn encourage a greater uptake of hyperconnected internet of things (IoT) applications. These changes to the commercial landscape will then drive stronger demand for integrated circuits (ICs) and hard disk drives (HDDs), especially for the large-capacity HDDs that are used in data center and cloud computing applications, where demand for big data applications is growing rapidly. In terms of consumer demand, the COVID-19 pandemic has also helped to precipitate a sudden explosion in working from home and distance learning that has then translated into stronger sales of PCs, notebooks, tablets and smartphones. Meanwhile, the shortage of ICs that was weighing on the industry (especially for use in auto assembly) should begin to dissipate in 2Q21, because production capacity has now risen on greater investment expansions from technology-leaders.
Overview
The Thai electronics industry has been the beneficiary of official support going back to 1972, when the government began to attract foreign capital inflows through the implementation of a range of tax and non-tax investment promotion strategies administered by the Board of Investment (BOI). Between 1972 and 1992, the government promoted the electronics industry as a growing contributor to the export sector, and partly thanks to government policy, foreign investors came to the country in greater numbers to set up production facilities for the manufacture of integrated circuits (ICs), printed circuit boards (PCBs), hard disk drives (HDDs), floppy disks, electric motors, and electric wires and cabling. Thailand was an attractive investment target for overseas players thanks to the country’s relatively low labor costs at that time, though its appeal as an investment target was also helped by the 1987 Plaza Accord[1], which led to a rise in the value of the yen and in the wake of this, many Japanese manufacturers relocated production facilities overseas, including to Thailand. By exploiting its low manufacturing costs, its geographical location at the center of the region, and following the establishment of the ASEAN Free Trade Area (AFTA) in 2004, the increase in the economic potential of the ASEAN zone, Thailand has been able to continue to attract international manufacturers, especially Japanese, Taiwanese and US corporations, and over time, these have steadily increased investment in the production facilities that they operate in Thailand.
However, the global electronics industry is marked by a constant whirl of technological change that perpetually disrupts the sector. This creates a challenging business environment and within the Thai electronics sector, it is only the major international corporations or Thai players that have formed joint-ventures with these that are able to compete successfully on the global stage. This then leaves most Thai operations to find a place for themselves as subcontractors manufacturing and assembling on order for the major players. But unfortunately, the result of this is that Thai labor remains relatively unskilled and Thai players are largely unable to add value by developing their own products, which is especially the case with regard to the production of ICs, PCBs, diodes and transistors. In addition, recent changes in the market for digital products mean that the product categories that have in the past been notably successful for Thailand are now losing their importance relative to other goods that are taking a more prominent place in global supply chains, including solid state drives (SSDs)[2] and some types of ICs and PCBs used in notebooks, smartphones and electronic gadgets. The domestic electronics industry is also being adversely affected by its only slow development of supporting technology and by rising labor costs, and the outcome of this is that overheads are rising, making the industry increasingly uncompetitive relative to producers in neighboring countries, such as China, Vietnam and Malaysia.
As of 2020, there were 615 registered manufacturers operating in the Thai electronics industry (Figure 1). These are split between two groups. (i) 31% of the total are classed as large manufacturers, most of which are either leading international manufacturers or joint-ventures between the latter and Thai companies, and these have access to both high technology and sources of funding. On the international side, these include Seagate Technology, Western Digital, Toshiba Semiconductor, and Canon HiTech. Thai manufacturers include KCE International, Tanin Elna, and SVI (Table 1). Most large manufacturers based in Thailand produce ICs, parts for HDDs, diodes and transistors, semiconductors, capacitors, resistors and PCB assemblies. (ii) The remaining 69% of players in the industry are SMEs, and these tend to face limitations with regard to their ability to develop their own technology, as well as being saddled with a weak negotiating position with regard to both downstream industries and suppliers of inputs and raw materials. Most of these companies produce PCB assemblies, capacitors, resistors, parts for printers and HDDs, cabling, computer parts and equipment, components for telephones, and so on.
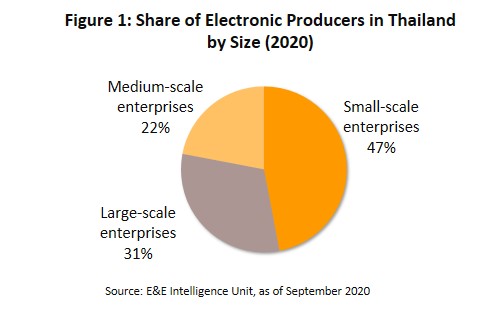
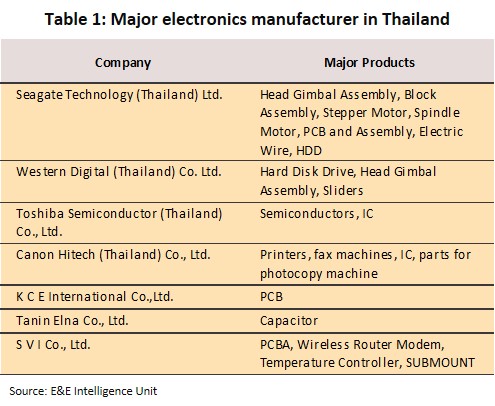
The Thai electronics industry is overwhelmingly focused on exports, with some 90-95% of output bound for overseas markets. Within the export segment, the most important products are HDDs, which comprise 29.3% of the value of all electronics exports (data correct in 2020), followed by other computer components, parts and equipment (21.9% of exports), ICs (19.6%), semiconductors, transistors and diodes (7.0%), PCBs (3.6%) and ‘other’ items (18.7%) (Figure 2). By value, 27.6% of exports are sold into the United States market, making it the most important export target. The US is followed in importance by Hong Kong (15.3%), the ASEAN zone (14.4%), the European Union (12.9%), China (10.5%) and Japan (8.7%) (Figure 3). The remaining 5-10% of output is consumed by the domestic market, where ‘other’ products are used to produce finished goods including telecommunication devices, equipment and parts used in auto assembly, home and office appliances, medical devices, and equipment used in a number of different industries.
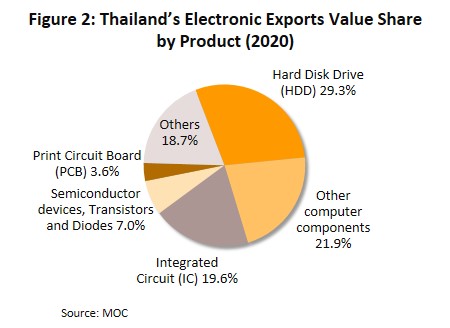
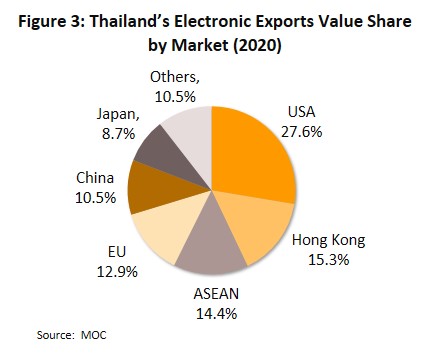
As of 2019, Thailand sat in 13th place in the global rankings of electronics production, but this gave the country just a 1.8% share of the value of the world exports. Globally, the most important sources of electronics exports are China (24.7% of the total) and Hong Kong (13.8%), followed by Taiwan, Singapore, South Korea and the US (Figure 4).
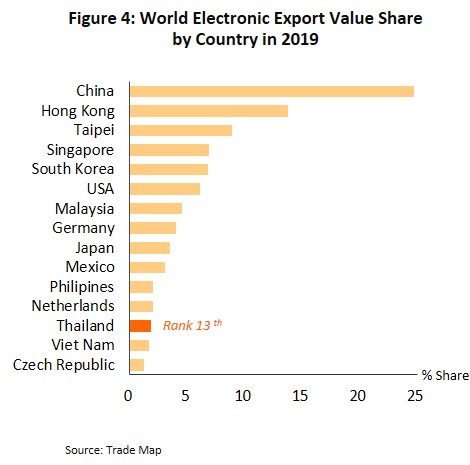
In 2019, the competitiveness of Thai electronics manufacturers in world markets shows that Thailand’s global market share is relatively low and growth is slowing. This situation has arisen because the majority of Thai electronics manufacturers do not invest heavily in research and development, and this then robs them of access to upstream technology, leaving players having to act as assemblers or as subcontractors for major global brands. Indeed, within Thailand, it is only a few widely-recognized world-leading international brands that in fact do invest in their own research and development, and this shortfall in R&D means that
Thai manufacturers are typically slow to react to the fast-evolving world of technology (electronic products generally have a relatively short product life cycle, and to recoup what can be heavy investment costs, manufacturers need to mass produce). Unfortunately, the outcome of Thailand’s weakening position in global electronics supply chains and the country’s declining competitiveness is that there is now a growing risk that international investors may relocate production facilities to more dynamic business environments (Figure 5).
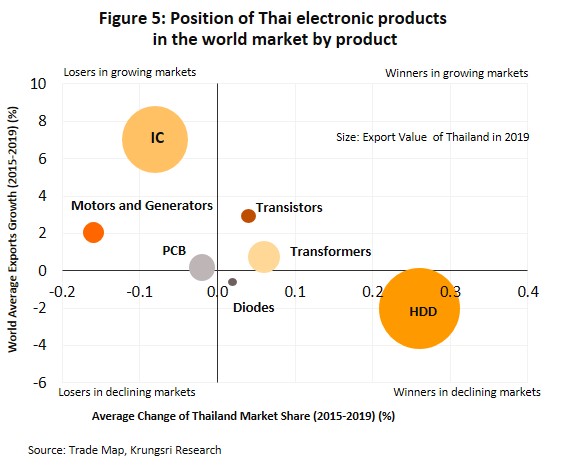
There are significant differences between the growth potential of exports of the various types of electronics goods produced in Thailand (Table 2). The most important export product categories are HDDs and ICs, which together account for 50% of the value of all exports of electronic products from the country. In particular, thanks to long-running investment in Thai-based production by international manufacturers that has lifted both the volume of outputs and of exports of computer parts, the country now occupies an important place in global computer supply chains with regard to HDD production. Because Thailand sits in a leading place in the global export rankings, Thai manufacturing underwent a change as it moved from low-value work (such as keyboard and screen assembly) to HDD production, which relies on higher levels of technology and skill. By contrast, although the majority of investment in Thai-based IC production has also been made by international manufacturers producing for export, this segment has evolved only slowly and this has negatively affected its competitiveness on world markets. Important features of these structural differences between the HDD and IC segments are thus outlined below.
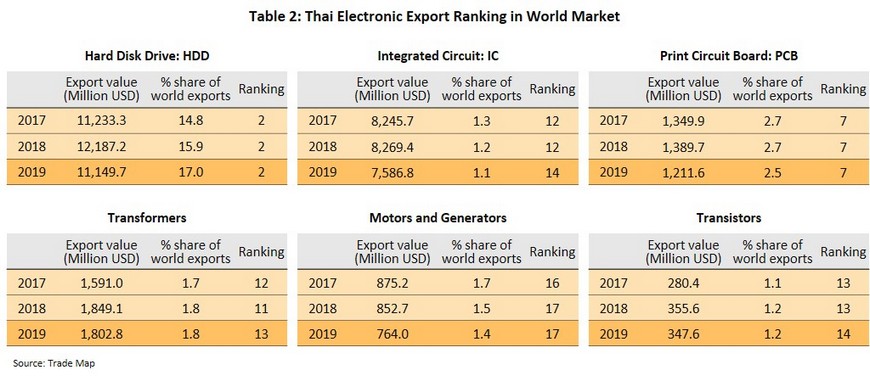
Hard Disk Drives (HDDs)
- The outlook for the HDD industry fluctuates with growth in the downstream electronics industry. And because 70% of HDDs are used in the assembly of personal computers (source: Technavio Insights, 2018), demand is heavily influenced by the volume of PCs distributed to the market.
- At present, over 90% of Thai-made HDDs are sold on export markets. Overall, the HDD segment accounts for almost 30% of all receipts for exports received by the Thai electronics industry. However, production is heavily dependent on foreign investment and this exposes the industry to changes in both the global economy and the investment policies of individual manufacturers, which are always looking for lower-cost production sites. At present, rising labor costs in Thailand are causing the country to lose ground relative to other countries in the region.
- As of 2019, Thailand held a 17.1% share of the global market for exports of HDDs, sufficient to put the country in 2nd place in the world rankings after China, which had a 26.5% share. Two of the world’s leading HDD manufacturers, Western Digital (WD) and Seagate, operate production facilities in Thailand.
- HDD production relies on a certain degree of technological mastery and a reasonably skilled workforce. And because investment has been rising in Thai-based production, the Thai HDD industry has become established and developed into a cluster of integrated HDD production. These exist at several different levels: (i) 1st-tier suppliers produce final goods (or direct materials), such as head-gimbal assemblies (HGAs) and head-stack assemblies (HSAs), motors, bases and covers, actuators, PCBAs, FPCs, and media; (ii) 2nd-tier suppliers manufacture components and parts (or indirect materials), such as suspension units, motor parts, sub-assemblies and coils; and (iii) 3rd-tier suppliers produce more minor parts. Both 1st- and 2nd-tier suppliers are typically international manufacturers or joint-ventures with these, and so they are therefore generally on a sound financial footing, able to market successfully, and have the ability to develop products that meet market demand. However, 3rd-tier suppliers are often Thai SME subcontractors that lack strong business connections and so these face difficulties adjusting to changing market circumstances. They are also often constrained by their weak negotiating position, which then exposes them to excessive pressure from larger 1st-tier and 2nd-tier players (Figure 6).
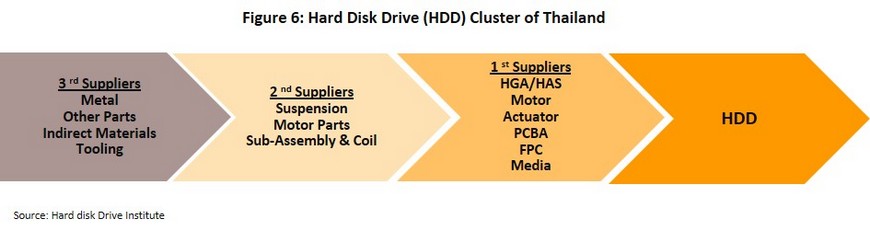
Integrated Circuits (ICs)
- The outlook for IC production is closely coupled with the situation in the semiconductor industry (a crucially important input into IC production). The latter tends to move with growth in the world economy and with that in particular in related industries (Figure 7), as well as with trends in investment in new technology within the broader electronics sector. As such, fluctuations in the state of the world economy and rapid technological progress, especially in consumer electronics such as smartphones and notebooks have been important factors in determining the direction of change for both the global and the Thai IC industry.
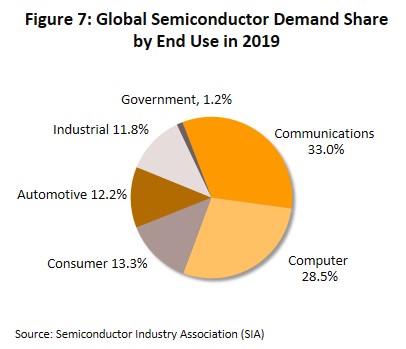
- Thai IC production is almost entirely for export markets (by volume, 95-99% of Thai output is sold into overseas markets). Thus, business conditions are largely set by a combination of the state of the world economy and the policies of individual companies with regard to offshoring in low-cost production centers and setting up local production sites as a stepping stone to penetrating regional markets. However, domestic factors have also had an impact on the market, most notably through the use of investment promotion strategies to attract foreign direct investment, which have now been running for many years.
- Major IC manufacturers active in Thailand include Hana Microelectronics, Stars Microelectronics, Maxim Integrated Products, Microchip Technology and Rohm Integrated Systems. Most of these are either international corporations or joint-ventures with the subsidiary of a major international manufacturer, such as the American companies Intel, AMD, Freescale, IBM and Spansion, the German Siemens and Infineon, the French ST Microelectronics, and the Japanese Sony, Toshiba, Renesas and Fujitsu. These players have ready access to financing, are masters of the relevant technology area, and carry out their own research and development of new products. By contrast, 30% of all Thai-based IC production is by Thai-owned IC manufacturers, most of which are SMEs that subcontract for the big players.
- Thai IC operators generally lack access to upstream technology since undertaking the research and development required for this can be prohibitively expensive, and so Thai manufacturers are instead reliant on high-levels of imports of materials and technology. Against this background, most Thai players therefore occupy a midstream position in global supply chains, focusing on labor-intensive processes such as IC packaging. However, Thailand’s advantages as a provider of low-cost labor are slowly diminishing, while the country has been somewhat unsuccessful in developing the workforce and knowhow necessary to move up the value chain, unlike the country’s other Asian competitors, including China, Taiwan, Singapore and Malaysia. As a result, Thailand’s competitiveness is declining and it is possible that international corporations may adjust their investment plans in light of this by moving production facilities to more attractive, lower cost sites in the region. As of 2019, Thailand’s share of the global market for IC exports was just 1.1% by value, placing the country in 14th place in the world rankings.
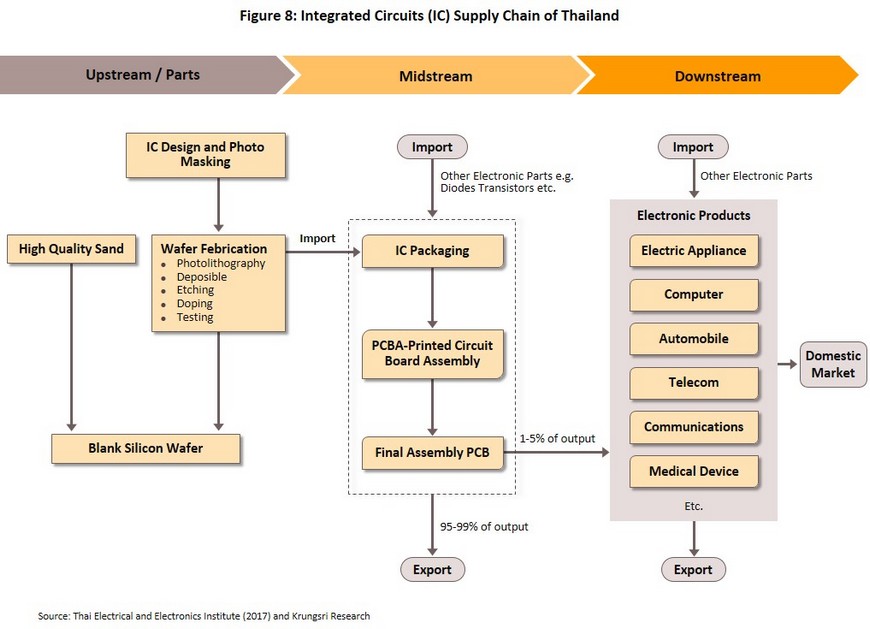
Situation
The Thai electronics industry is heavily dependent on exports, and the country is now home to a large number of international manufacturers, though the industry has had mixed fortunes. Over the period 2011-2019, while the value of exports of HDDs grew by an average of 10.9% per year, those of ICs shrank at an annual rate of 0.5% (figures are compound annual growth rates).
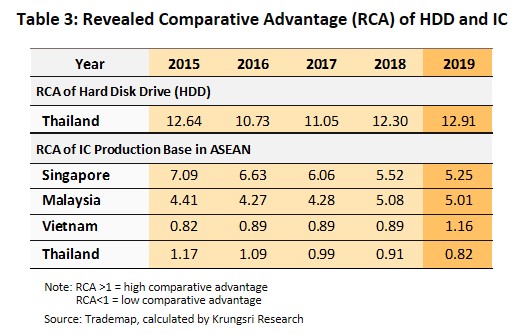
- Growth in the value of exports of HDDs has outpaced that of other product categories in the electronics industry thanks to continuous investment in in-country HDD production that has established Thailand as a major supplier of world markets. Changes in the fortunes of HDD producers over the past decade are outlined below.
- 2011-2019: In late 2011, Thai HDD production was severely disrupted by the extensive flooding of Bangkok and the central region of Thailand. This brought productions of and shipments of HDD and parts to an almost complete halt. And because the country was at that time the world’s principal source of HDDs, supply to world markets tightened significantly. In response, manufacturers looked to disperse production across a wider spread of the ASEAN zone as they tried to reduce the risk of future supply disruption (e.g., from another natural disaster) that might arise from an overconcentration in any one area. Thus, Toshiba sold all its Thai-based HDD production capacity to Western Digital (WD) and moved instead to the Philippines, while WD moved some capacity to Malaysia, and this then depressed Thailand’s HDD manufacturing production index (MPI) over the years 2011 to 2016. However, strong demand that outran supply growth and the higher prices commanded by new, higher-capacity drives helped to pull the value of exports in the opposite direction. Following this, in 2017-2019, the business environment for HDD manufacturers improved again as WD and Seagate (which together command an 80% global market share by value; Figure 9) changed tack and decided to use Thailand as their main location for producing HDDs for export, closing facilities in Malaysia and China and instead increasing capacity in Thailand. Unfortunately, while from the supply side the situation has improved, global demand for HDDs is softening. Worldwide, sales of PCs fell steadily between 2012 and 2018 as office workers increasingly switched to using notebooks and consumers spent more time on their smartphones and tablets, which use SSDs, not HDDs. HDD producers have done their best to fight against these trends, developing lightweight hybrid-HDDs that have similar qualities to SSDs for use in notebooks and tablets, as well as producing high-capacity HDDs for use in cloud computing applications, and these moves have helped Thai players preserve their market share.
- 2020: The MPI for the HDD industry slipped 2.8%, in line with a 2.0% fall in the value of exports to USD 10.7 billion, though it is worth noting that exports of HDDs have remained above USD 10 billion for the past 4 years. This was driven by the impact of COVID-19 on the global economy and a weakening in demand for HDDs, with global sales of PCs (most of which still use HDDs) growing by just 1.8% in 2020, compared to the 22.5% jump in the number of notebooks distributed worldwide (source: Trend Force, January 2021). This disparity in demand is explained by the much greater preference for notebooks shown by consumers when working from home or learning online.
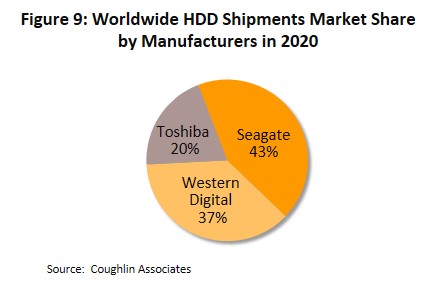
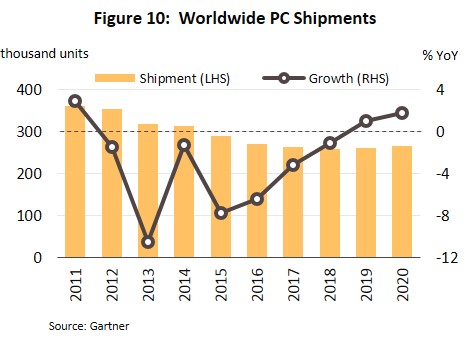
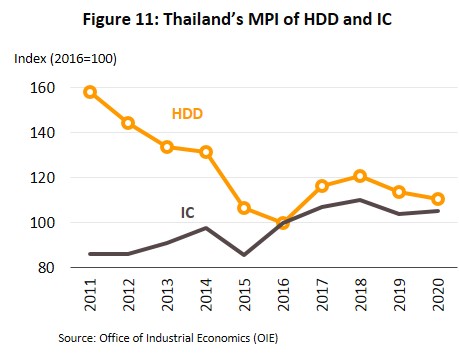
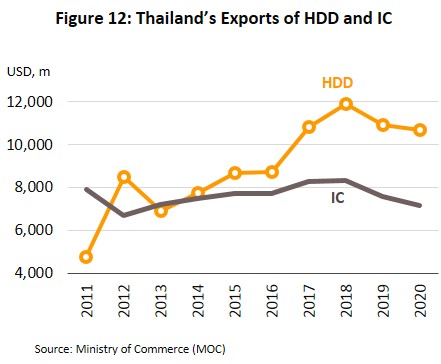
- The impacts of the past decade on Thai IC manufacturers are described below.
- 2011-2019: As with HDD manufacturers, the Thai IC industry was badly affected by the flooding of 2011, and production partly halted. Output was slow to pick up again, encouraging some buyers to switch to sourcing goods from suppliers in other countries, while a weakening of the world economy undercut global markets for ICs, especially in China. Given this, 2011 exports of ICs fell by 1.9% and then by another 15.4% in 2012. The market rebounded to growth of 7.9% in 2013 but this then slowed again before going into reverse, dropping to 4.0%, 3.0% and -1.2% over each of 2014, 2015 and 2016. This turbulence was driven by two main factors: (i) Conditions became choppy for the electronics industry, which then encouraged manufacturers to exercise greater care over their stocks of inputs, including their holdings of semiconductors. And because of this, global sales of semiconductors grew at an annual average rate of 3.4% over 2014-2016, compared to 9.3% through the period 2010-2013. (ii) Some manufacturers of ICs and component parts aw well as some major buyers of ICs within the electronics industry moved production from Thailand to other countries[3]. In the years 2017 to 2019, the outlook for Thai IC manufacturers tracked movements in the global market for semiconductors. In 2017 and 2018, electronics went through a boom period as the global economy grew and internet connectivity spread. This then boosted demand for electronics, helping the semiconductor market to revive as stock levels rose to historic highs in 2018 (Figure 15). However, in 2019, semiconductor sales were hit by the US-China trade war[4] and the widespread effects of this on the world economy and demand for electronic products. Given this, the value of Thai exports of ICs went through a period of instability, rising by 7.1% in 2017 and then by just 0.8% in 2018, before contracting by 8.9% in 2019.
- 2020: Thai IC production struggled through the year as MPI of the industry edged up only 1.0% and the value of IC exports slipped 5.7% to USD 7.16 billion. Producers were hit by pandemic-driven supply chain disruption as many countries, including China, South Korea and other trade partners, imposed temporary lockdowns that reduced output and made the transport of goods problematic. In particular in 4Q20, semiconductors (the key component in IC production) also became increasingly difficult to source as demand for electronics equipment jumped on the surge in working from home and online study. Thus, by volume, global distribution of semiconductors grew 6.0% in 2020 (compared to a fall of 12.3% in 2019) but expanding supply to meet this is a slow, capital-intensive process.
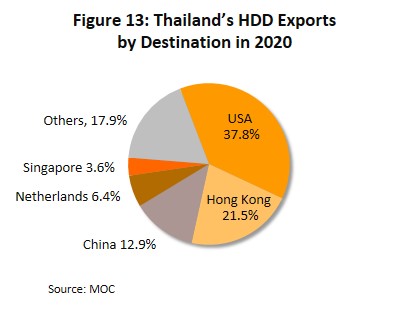
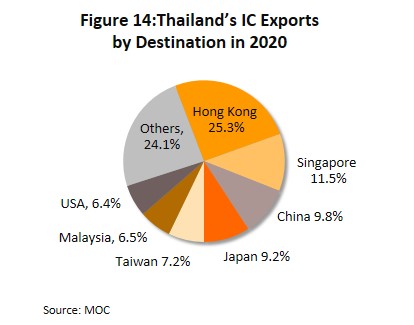
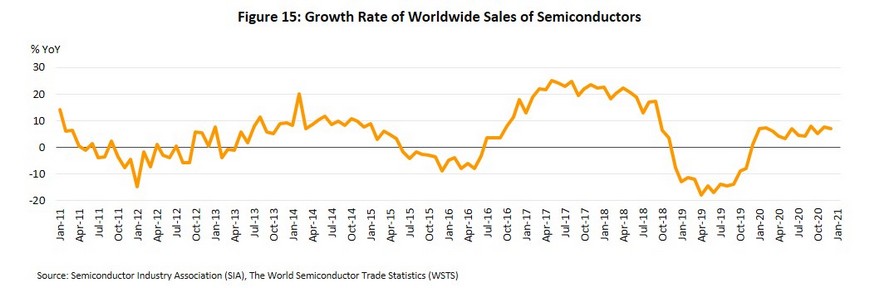
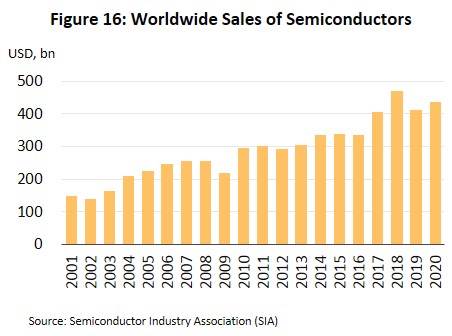
Outlook
The outlook for Thai electronics manufacturers should generally improve over the three years from 2021 to 2023 as demand grows with recovery in the world economy (the IMF sees global growth reaching 5.5% in 2021 and 4.2% in 2022). Better business conditions will be helped by the extensive use of stimulus measures in many countries and success in the hunt for COVID-19 vaccines. Following their approval, the rollout of national vaccination programs since the close of 2020 will now help to suppress the spread of the pandemic and then to reduce the economic impacts of shutdowns, while the increase in demand for electronics goods during the period of lockdown has left global stocks depleted, and the need to refill this empty warehouse space will feed into stronger production. The outlook for the individual HDD and IC segments is given below.

- Through the three years from 2021 to 2023, output of HDDs by Thai manufacturers will tend to grow slightly, though the value of exports is forecast to rise by an average of 3.0-4.0% per year. The HDD segment will be boosted by the two factors. (i) Demand for high-capacity 3.5-inch HDDs will continue to strengthen for use in cloud computing and data center applications, where HDDs are used to store the huge amounts of information used in big data analysis. This market is undergoing strong growth that has been lifted further by the outbreak of COVID-19 and the big step forward in uptake of cloud computing services that was needed to meet the sudden expansion in working from home and distance learning[5]. (ii) HDD manufacturers are continuously developing new techniques to extend the working lives of HDDs and to expand their storage capacity, and rapid advances in these areas are helping to bring down the price of HDDs per storage unit. These new production and storage technologies rely on a range of breakthroughs, including helium hard drives[6], shingled magnetic recordings (SMRs)[7], heat-assisted magnetic recordings (HAMRs)[8] and microwave-assisted magnetic recordings (MAMRs)[9]. Taken together, these should help Thai players to preserve their share of HDD export markets. Nevertheless, a number of headwinds will limit the room for growth in the HDD segment. (i) Demand for HDDs for use in PC assembly will tend to weaken globally and IDC (September 2020) predicts that through 2021-2023, the number of PCs sold worldwide will fall by 2.0-4.0% per year. (ii) HDD manufacturers will have to contend with greater competition from alternative products, most notably SDDs that can be used in place of the 1.8-inch (now discontinued) and 2.5-inch HDDs that are found in notebooks and some other portable electronic devices. In these segments, SDDs are therefore displacing HDDs (Figure 18), while tape drives continue to be used for permanent low-cost data storage or backup in situations where costs are more important or where access is only infrequent, such as in some server and cloud computing use-cases (Figure 20).
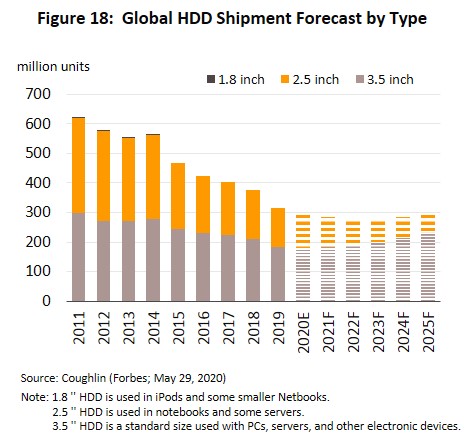
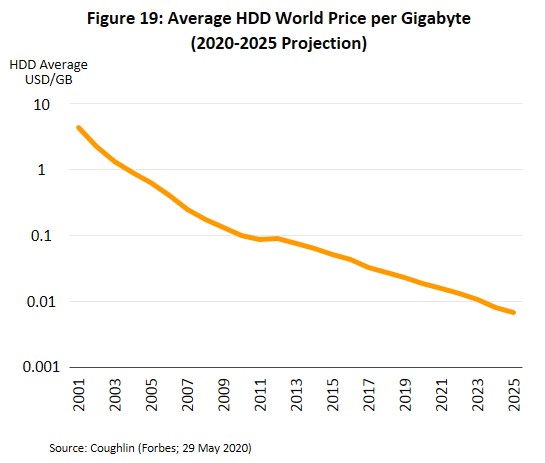
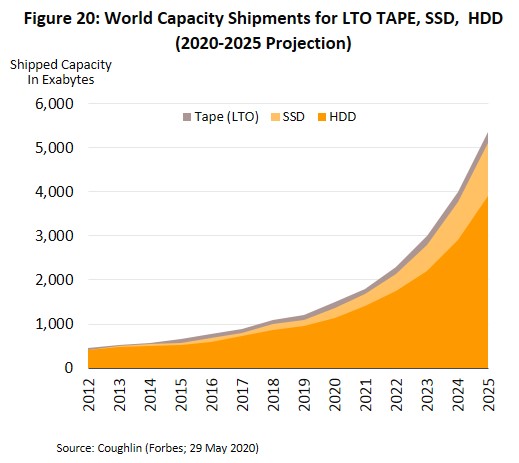
- The outlook for manufacturers of ICs over the period 2021 to 2023 is generally sunny, and the value of exports is expected to bounce back to average annual growth of 6.0-7.0%. This is in line with predictions from World Semiconductor Trade Statistics (WSTS) that sales of semiconductors to the global market will rise by 8.4% in 2021, following growth of 6.0% in 2020 (Figure 21). The Semiconductor Equipment Association of Japan (SEAJ) also sees the market value of semiconductor manufacturing equipment sold by Japanese companies based both in Japan and overseas strengthening by 7.3% in 2021 and then by 5.2% in 2022, having already risen by 8.2% in 2020 (Figure 22). This positive business environment will be supported by: (i) the surge in working and learning at home that national lockdowns brought about and which then translated into much heavier demand for consumer electronics, such as PCs, notebooks, tablets, games consoles and smartphones; and (ii) the effects of global technological megatrends: (a) The development of auto technology, and in particular of electric and autonomous vehicles, will carry with it greater software requirements that will in turn require the use of a larger number of ICs (up to 150 compared to some 40 in a standard modern car); and (b) the new generation of 5G-compatible smartphones use around 40% more ICs than equivalent 4G devices. The rollout of 5G technology is expected to accelerate shortly, especially in developed economies, and thus global investment in 5G networks’ infrastructure backbone is projected to increase by 19% in 2021 (source: Gartner, July 2020). This growth in 5G networks will also then spur the take-off of the internet of things and this will feed into stronger demand for electronics goods in general and for ICs in particular. On the downside, the market has recently been hampered by a shortage of supply of ICs caused by an acceleration in demand at the end of 2020, but this should subside from 2Q21 as stronger investments begin to translate into an expansion in manufacturing capacity in countries that are technology-leaders (Box 1).
Box 1
Shortages of ICs should begin to wane from 2Q21 onwards thanks to stronger investments and an expansion in production capacity in technology-leading countries.
The shortage of ICs and chips that has troubled the market since the end of 2020 has been triggered by a sudden increase in global demand that was itself caused by two main factors: (i) The COVID-19 pandemic and subsequent need for lockdowns and social distancing measures brought with it an upsurge in distance working and education, and with this, consumer demand for electronic devices jumped. (ii) The simultaneous development of new 5G-compatible electronic devices and smart cars is driving a substantial strengthening in demand for ICs. However, in addition to demand-driven disruptions, supply-side factors have also affected the market. (i) Output of semiconductors, the main input into production of ICs, is insufficient to meet demand. And, because chip production (from etching the silicon through to manufacturing the wafer) is such a technically-demanding process, rectifying this situation by expanding existing facilities or constructing new ones takes an extended period of time and consumes significant sums of money. (ii) Only a few players have the resources and technical expertise to manufacture chips at scale. As such, a significant proportion of global capacity is controlled by just two companies: Taiwan Semiconductor Manufacturing (TSMC), a Taiwanese company with a 54% share of the global market for ICs, and Global Foundries, a US company with an 11% market share (BottomLiner 2016). (iii) Some electronics manufacturers and auto assembly plants have tried to hedge against the risk of shortages by hoarding supplies of ICs.
However, Krungsri Research expects that these problems will begin to subside in 2Q21. This view is supported by analysis carried out by HIS Markit in January 2021, predicting that shortages of ICs used in auto assembly will cut global production by 672,000 units in 2021, or just 0.73% of 2019 world output (91.8 million vehicles), and that supply constraints will begin to ease in February-March as IC manufacturers in many countries ramp up production. At the start of 2021, governments in countries with significant indigenous technology industries (e.g., China, Taiwan, the US, and Japan) responded to the chip shortage by encouraging additional investment in an expansion of domestic semiconductor and IC production capacity. Companies affected by this included Semiconductor Manufacturing International (SMI), China’s biggest manufacturer of ICs, which added an additional 45,000 chips/month of capacity, and TSMC and United Microelectronics Corporation (UMC) from Taiwan, which added respectively 60% and 50% to their potential output (source: The Loadstar, the supply chain news link, the United Kingdom, February 2021). Technology leaders are also investing in the facilities needed to produce third-generation semiconductors that are made from silicon carbide and gallium nitride. These substrates have unique physical and chemical properties that make the chips more suitable for use in some high-tech applications, such as in electric vehicles, and production of these will begin in 2021 (source: Aljazeera.com) at plants operated by companies including CREE (US), Sumitomo Electric Industries (Japanese), Sanan Optoelectronics (Chinese) and Electronics Technology Group (also Chinese). Among the same set of countries, though especially in the US and China, efforts are also underway to increase security of supply by sourcing ICs from a much wider range of suppliers, thus maintaining a set of reserve sources in different countries. In addition, these governments are increasing the potential of domestic suppliers to assume world-leading positions by attracting leading IC manufacturers (e.g., TSMC) to invest in new production facilities in the form of public-private partnerships (source: Bloomberg, January 2021 “The world is dangerously dependent on Taiwan for semiconductors”).
Krungsri Research view
Revenue for Thai electronic manufacturers is forecast to return to growth over 2021-2023, helped by recovery in the world economy that will support stronger demand and by the development of new technologies following global megatrends.
- Manufacturers of HDDs and components: For players in this segment, revenue should strengthen with demand in export markets. Sales of high-capacity HDDs will rise with growth in cloud computing, and this together with ongoing technological innovation will help Thai players maintain their market share. Nevertheless, manufacturers will have to face negative pressures on revenue growth arising from the steady decline of PC sales globally and the effects of this on demand for HDDs, as well as the increasing tendency of SSDs to be used in place of HDDs. Players that operate as subcontractors will also need to develop production processes in line with rapidly changing technologies, and this may call for increased levels of investment that will translate into higher production costs. Unfortunately, because most subcontractors find themselves in a weak bargaining position, their ability to pass on higher overheads is limited and as such, this may erode profit margins.
- Manufacturers of ICs and components: The value of exports of ICs is expected to rise steadily on stronger sales of semiconductors. This can be attributed to the COVID-19 pandemic and the sharp boost that this has given to demand for electronic goods, in particular those connected to the internet of things and to data center applications. In addition, the development of smart cars and 5G technology is moving forward rapidly and as these become much more widespread (an event that is underway, judging by the increases in global investment in 5G networks that are planned and that will be needed to meet a surge in IoT applications), demand for electronic goods, and especially ICs, will tend to rise. Despite these positive factors, though, Thai IC manufacturers and subcontractors will need to overhaul their production lines as they adapt to the constantly and rapidly changing technological landscape and to greater demand for more complicated ICs, and this will add to their investment costs. At the same time, Thai IC manufacturers, which tend to be subcontractors focusing on labor-intensive operations, are having to contend with stronger competition from countries such as Vietnam that enjoy lower labor costs than Thailand and that are increasingly improving their domestic production. As such, Thai competitiveness and revenue is at risk of being eroded.
- Manufacturers of PCBs and components: Revenue will tend to increase with the higher value of exports. Technological change will affect the development of goods such as cars, electronics, machinery and electronic appliances, which will increasingly form part of smart, artificial intelligence-enabled networks connected to one another through the internet of things. This will then naturally stoke stronger demand for PCBs, but at the same time, this segment will face the same set of challenges as those confronting players in other parts of the industry. Thus, Thai engagement in global supply chains tends to be in the form of labor-intensive subcontracting work, but Thai labor costs are rising, pushing up overheads and lessening the country’s competitive advantage relative to players in China, Vietnam, and the Philippines, where labor costs are more attractive.
[1] The Plaza Accord was agreed in 1985 and aimed to address the global consequences of the depreciation of the yen, which had led to a significant rise in Japanese exports and thus to trade imbalances worldwide. In response to this, the other G5 nations (the US, the United Kingdom, Germany, and France) pushed for an increase in the value of the yen, but this raised production costs for Japanese manufacturers. These were thus incentivized to relocate outside the country as they looked to retain their competitive advantage by slashing their overheads.
[2] SSDs are a type of data storage device. These are composed of a controller chip and the memory storage material itself, which allows the SSD to act as a kind of flash memory. This differs from HDDs, since the latter store data on a magnetic platter, and this difference allows SSDs to be lighter, faster and more hard-wearing than the HDDs that they are slowly replacing
[3] Sanyo Semiconductor moved production to the Philippines, Maxon Systems relocated its mobile phone parts production to Cambodia and LG Electronics shifted production of flat-screen TVs to Vietnam.
[4] The US hiked customs duties on imports of Chinese ICs and semiconductors from 10% to 25% with effect from August 2018. China responded to this by mirroring these increases in the duty placed on imports of US ICs and semiconductors from September 2018.
[5] Gartner forecasts (September 2020) that investment in infrastructure-as-a-service (laaS), a type of cloud computing service, will have grown by 13.4% in 2020 to a total value of USD 51.4 billion, and will then expand by another 27.6% to USD 64.3 billion in 2021.
[6] Helium hard drives contain helium in place of air inside the drive mechanism, which then increases the efficiency of the spindle motor that drives the magnetic platter, cutting power consumption by 49% and reducing the drive’s temperature by an average of 4 degrees Celsius. In addition, a helium atmosphere reduces disk vibration, allowing disks to be packed closer together and raising the maximum number of platters to 8 from the current limit of 5. As such, disk capacity can be substantially improved.
[7] Shingled magnetic recording (SMR) works by recording data in tracks on the surface of the magnetic disk that are smaller than standard and that overlap slightly in the manner of roofing shingles (from which the technique takes its name). By using this technique, individual disks can now store up to 1.4 TB per square inch.
[8] Heat-assisted magnetic recording (HAMR) uses a laser on the read-write head to temporarily heat the surface of the drive (manufactured from an FePt platinum alloy). This makes the disk material much more sensitive to magnetic effects and this then increases the disk capacity to 5 TB per square inch, but because the technique requires that the disk be heated to 400 degrees Celsius, its lifespan is substantially reduced.
[9] Microwave-assisted magnetic recording (MAMR) uses a spin-torque oscillator (STO) to direct a microwave to the surface of the drive that then encodes data magnetically on the disk. This allows data to be recorded more tightly and boosts capacity to 4 TB per square inch.